TURBO CHARGERS
This precisely and fully automated laser cladding process accompanied with its measurable metallurgical advantages makes it ideal to recondition components such as:
– Turbo charger turbine shafts
– Turbo charger casings
– Turbo charger bearing housings
– Turbo chargers end covers
Turbo charger component repair with Laser Powder Cladding Technology
Our innovative surface modification technique guarantees an unparalleled bond between the base material and coating material, overcoming challenges associated with traditional welding.
With low heat input and minimal dilution levels, our method offers a cost-efficient and effective approach to revitalizing turbo charger parts.
Key Features:
Enhanced Wear Resistance: Laser powder cladding elevates wear resistance to new levels, ensuring longevity and durability.
Improved Corrosion Resistance: Experience superior corrosion resistance, addressing vulnerabilities seen in conventional welding.
Optimized Thermal Stability: Our technique enhances thermal stability, a critical factor for performance in varied environments.
Increased Conductivity: Benefit from improved conductivity, optimizing the functionality of the coated components.
Reduced Distortion and Stress Cracking: Minimize distortion and stress cracking, ensuring structural integrity throughout the welding process.
Why Choose Our Laser Powder Cladding Facility?
Cutting-edge Equipment: Our facility is equipped with state-of-the-art technology, ensuring precision and efficiency.
Expertise: Our team brings extensive expertise to every project, guaranteeing outstanding results.
Transformative Potential: Witness the transformative potential of laser powder cladding in the welding industry through our exceptional outcomes.
Embark on a journey towards excellence in welding and surface engineering with us. Explore the limitless possibilities of laser powder cladding technology for bronze welding, setting new standards for performance and durability.


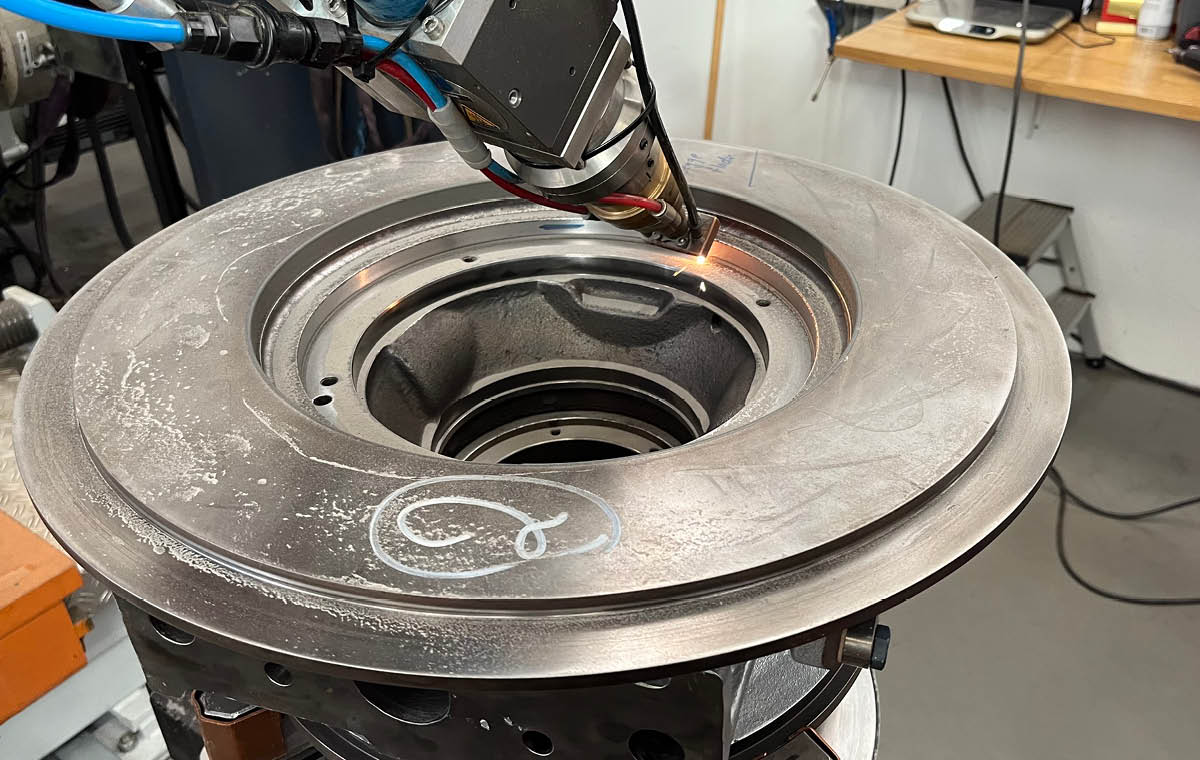
